Owners of ready mix concrete batching plants may make or lose money even in the same region and the same time period. Obviously, this is not a mere issue of luck. Running a ready-mixed concrete mixing plant in the most cost efficient way entails scientific management of your staff and planning of the whole operation process. Here Haomei would like to share some practical methods about cost reduction in concrete mixing plant management, raw material management, production, transportation and so on.
Improvement of management system
From the purchase of raw materials to the production, sales, transportation, and pouring of concrete, this process must be standardized. Every matter needs to be dealt with by different people, and the boss does not need to do everything by himself. Otherwise your staff will be afraid of doing everything, which leads to rise in management cost.
Raw material cost control
Suppliers: Find a few more suppliers and shop around. You can not only buy the cheapest raw materials, but also prevent the sudden out of stock of one of them, which will affect the production of the ready-mixed concrete batching plant. In addition, considering the transportation time and cost, priority should be given to selecting raw material suppliers that are geographically closer to the mixing station.
Purchasing time: For example, there is a winter break in the northern region every winter, and the price of raw materials at this time will be lower. Therefore, calculating the demand for raw materials for the second year in advance and buying them when the price of raw materials is low can save a lot of cost.
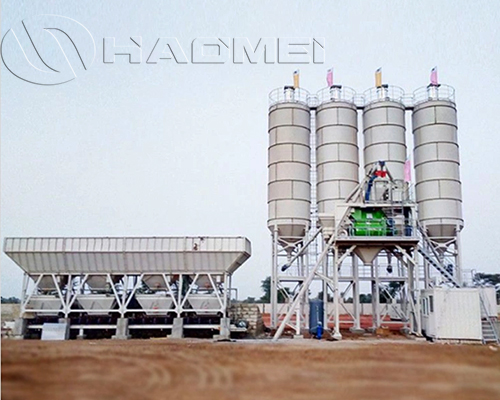
Policy information: According to local policy information, it is also an effective method to predict the price trend of raw materials and prepare the material in advance before the price rises.
Concrete production process
How to save the cost of raw materials: The most effective way is to improve the proportion of various raw materials under the conditions of concrete strength that meets the needs of the construction party, so as not to waste every minute of the material.
How to control concrete slump: First, increase the amount of admixtures to reconcile the slump of concrete. Second, with the admixture unchanged, reasonably increasing the amount of other raw materials can also control the slump of concrete. Which method to use depends on the local raw material prices and analyze the most cost-saving plan.
Recycling of resources: For example, the residues washed out of the mixer truck can be separated into aggregates for reuse, and the water can also be reused by re-filtering.
Mixer truck transportation management
The focus is on the control of fuel costs. It is necessary to regulate the mixing truck loading time, transportation time, and waiting and pouring time on the construction site.
The fuel consumption of the mixer truck when it is full is several times that when it is empty. Therefore, it is necessary to reduce the daily heavy-load waiting time of each truck and control it for about one hour to meet the cost control of the ready mix concrete batching plant.
Vehicle management, personnel management, production process optimization, strengthening cost control in production links, improving the application level of mix ratios, and strengthening the recovery rate of materials, all these are the key to controlling the cost of a ready mix concrete batching plant.